BLOG
The Evolution of Edgebanding

The Evolution of Edgebanding: From Wood Strips to High-Tech Edges
What is edgebanding?
Edgebanding is the narrow strip used to cover the raw edges of wood-based panels like particleboard, MDF, and plywood. It protects the core, enhances durability, and creates a clean, uniform and finished look. Today, it’s found on nearly every modern furniture piece; from kitchen cabinets to office desks.
Early Beginnings: Wood and Veneer Edges
Before engineered panels, furniture was made of solid wood and didn’t need separate edgebanding. But with the rise of plywood and particleboard in the early 20th century, furniture makers began gluing thin wood or veneer strips to cover exposed panel edges a labor-intensive, manual job.In the 1950s, early plastic solutions like T-moldings appeared. These were flexible vinyl strips inserted into panel grooves; a quick fix, but with limitations.
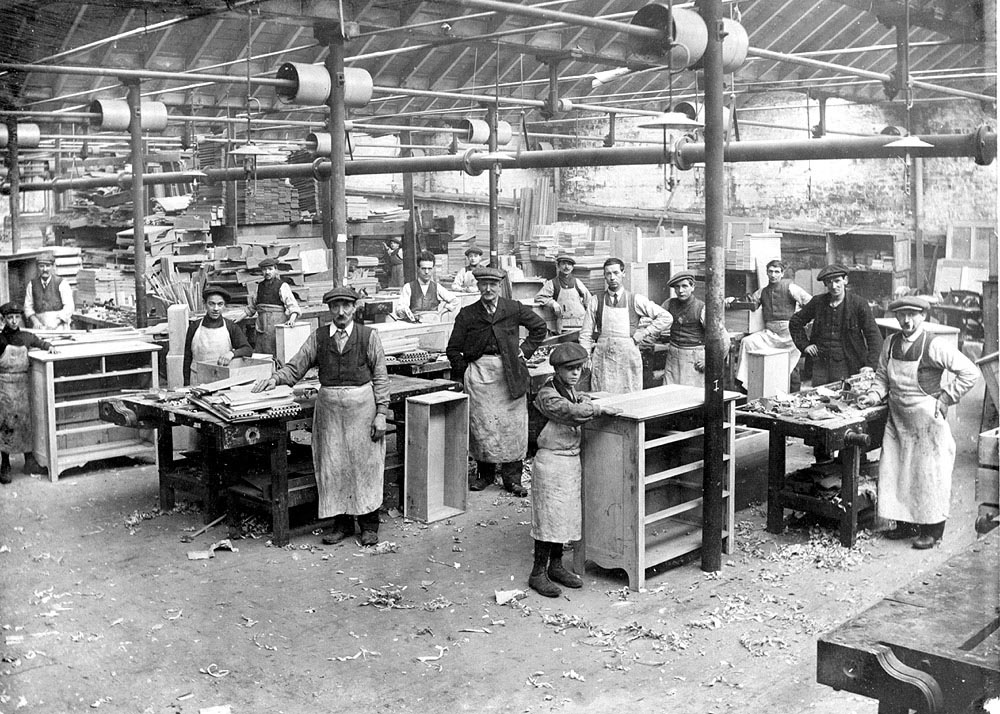
Industrial Breakthrough: PVC and Hot-Melt Gluing
The real transformation came in 1954, when Germany’s Döllken started producing PVC edgebanding, and later, in 1962, when HOMAG introduced the first automatic edgebanding machine using hot-melt glue. This made it possible to mass-produce edgebanded furniture at scale, marking the start of modern edgebanding.PVC quickly became the dominant material: flexible, colorable, and cheap. It allowed for easy matching with laminate surfaces.
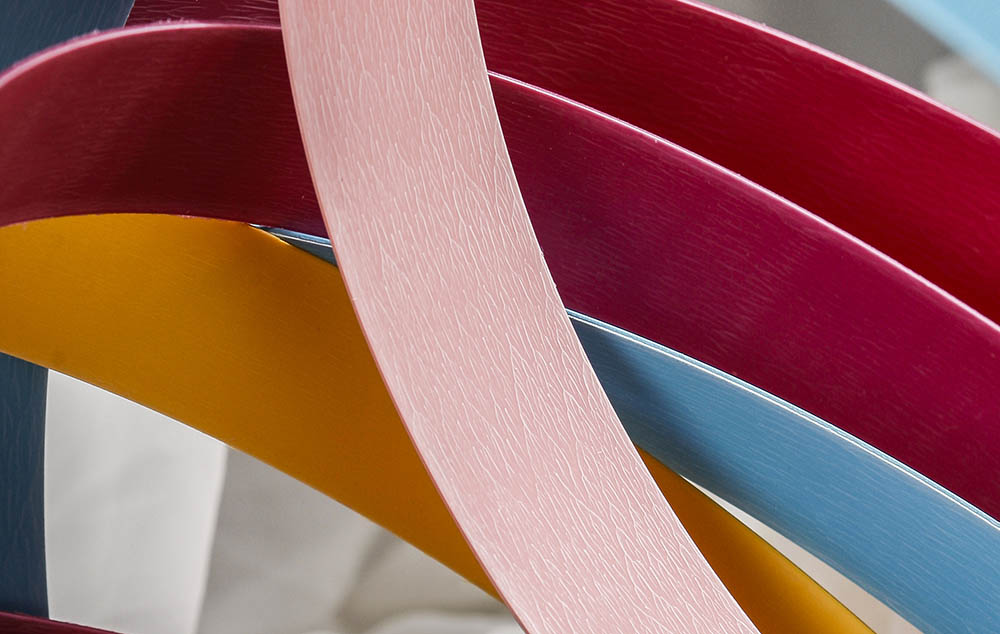
Material Expansion: Veneer, Melamine, PVC, ABS, PP, and Acrylic
By the 1970s–80s, global furniture demand exploded, especially for panel-based modular furniture. Today, the varieties of edgebanding are below:
• Melamine edgebanding (paper-based) offered a cheap solution and also with a DIY option.
• Wood veneer edgebanding; still the ultimate choice for premium cabinetry.
• PVC edgebanding is still dominant product in the whole world.
• ABS and PP (polypropylene) emerged as eco-friendly plastic alternatives to PVC, especially in Europe.
• PMMA Acrylic (3D edges) became a go-to for glossy, high-end furniture with a glass-like finish.
Today, manufacturers offer a full range: thin tape, thick impact edges, textured or smooth, matte or glossy.
Modern Innovations: Laser & Zero-Line Edging & Changing to PUR
From the 2010s, high-end furniture pushed for seamless edges. This led to laser and hot-air edgebanding, using edgebanding with a special pre-applied layer that melts and bonds without visible glue.This zero-joint technology gives a perfectly clean look and improves resistance to moisture, heat, and wear. Today, there are many branding, including TECE, to offer this range.
Today, many furniture producers are avoiding zero joint technology because furniture industry wants to remain as simple as it can. Yet, a strong bonding is a must in bathroom and kitchen. To this end, many companies are opting for PUR glue solutions where any edgebanding can be used.
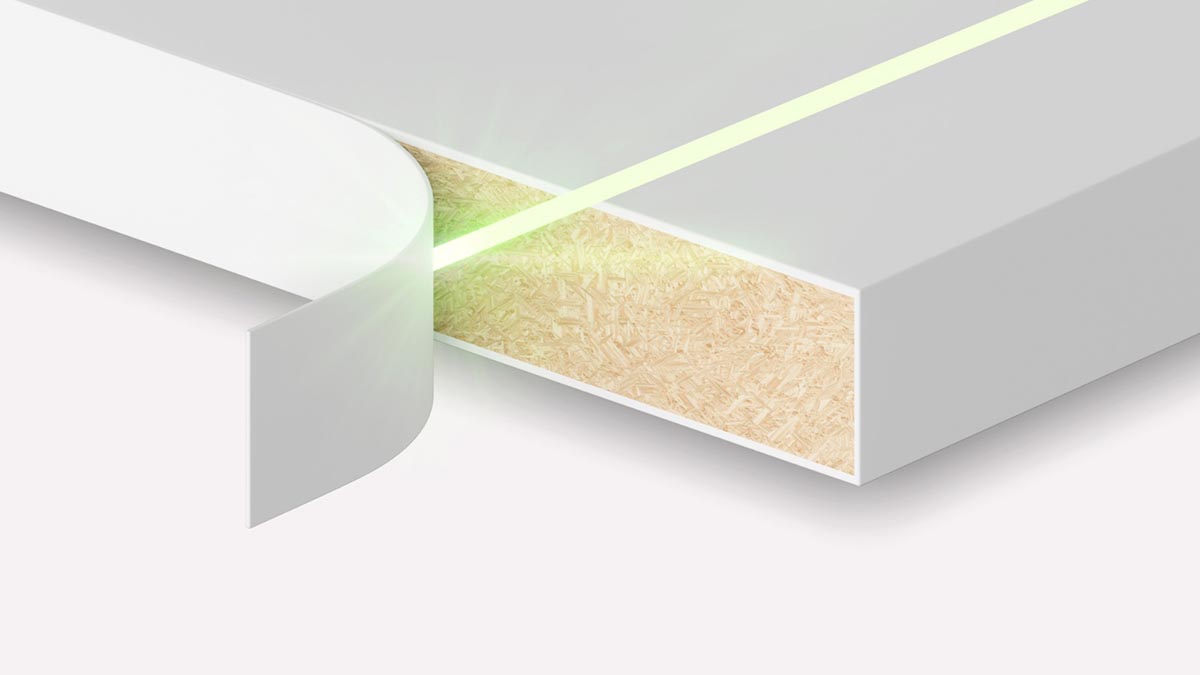
Design Trends and Functional Needs
Edgebanding now reflects design:• Thick edges (2–3 mm) are used in commercial or durable products.
• Thin edges (0.4–0.8 mm) are trendy in minimalistic, modern furniture.
• Contrasting colors or metallic finishes are used as design accents.
• Embossed textures help match realistic wood, stone, or matte panels.
Beyond design, edgebanding improves product life. A properly sealed edge prevents moisture damage — essential in kitchens, bathrooms, and hospitals.
Sustainability and the Future
Environmental focus is reshaping the industry:• ABS and PP are promoted over PVC due to recyclability and cleaner incineration.
• Some brands use recycled plastic in their edgebanding. TECE is going to be the leader in this end. This will be the game changer in the long run. And edgebanding produced 80% from recycled products.
• New bio-based materials like PLA (corn-based) show future promise. Yet, due to costing of raw materials, this is not going to be a real game changer.
• From our opinion, PUR is going to play a major role in the future with its strong bonding.
Also, better edging extends furniture life reducing landfill waste and supporting circular economy goals.

Conclusion
From handmade wood strips to high-tech laser edges, edgebanding has evolved into a crucial, high-performance component of furniture manufacturing. It reflects trends in design, materials, sustainability, and global trade. Wherever there’s a panel, there’s a story at the edge and today’s edgebanding makes sure that edge is strong, seamless, and stylish.And as TECE, we have been following this evolution at each stage, and we will do so for the future as well. Because edgebanding is not just our source of income, it is our lives.
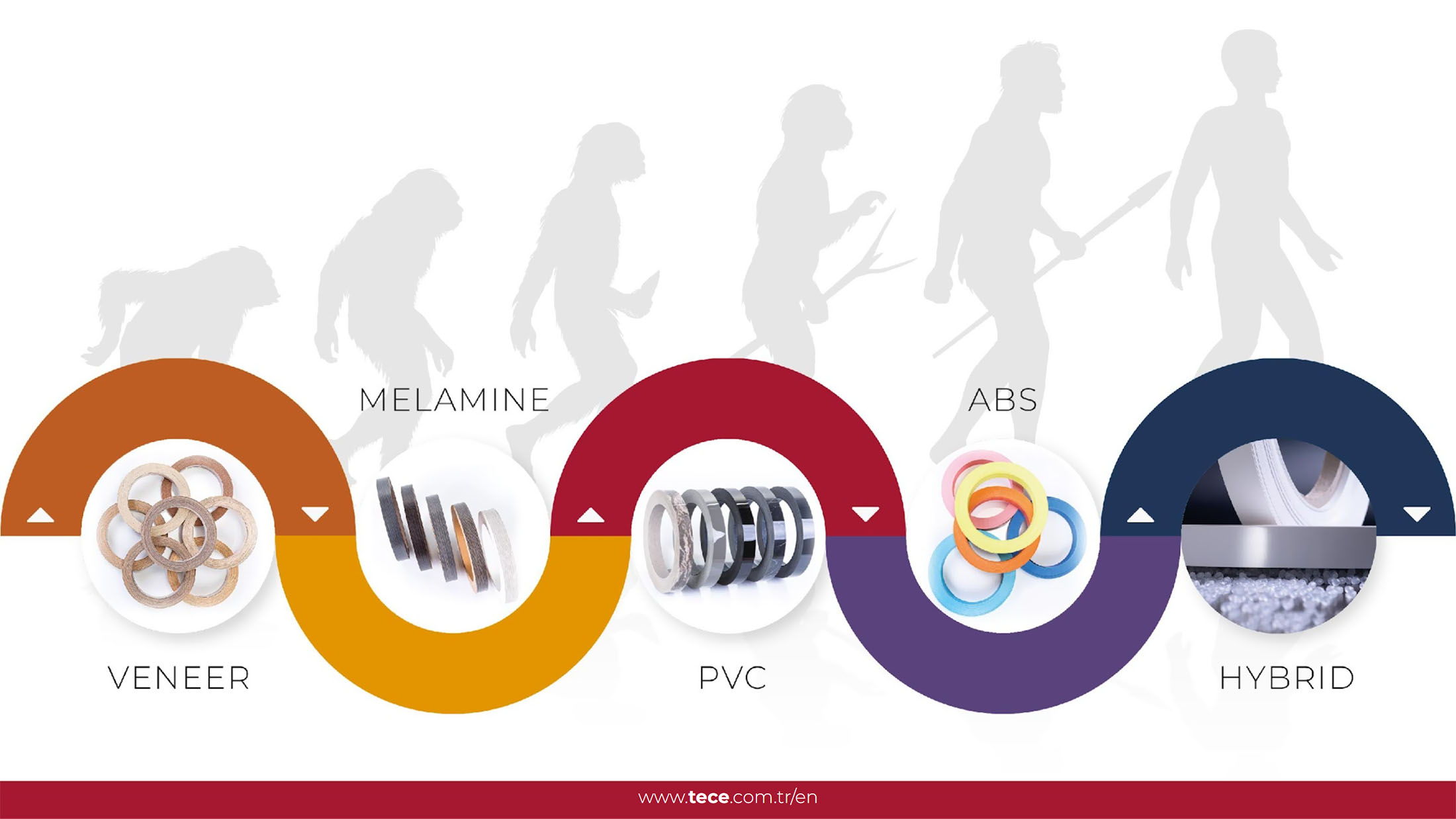